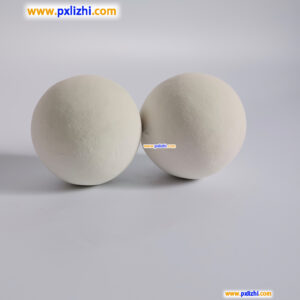
# Inert Ceramic Ball Applications in Industrial Processes
## Introduction to Inert Ceramic Balls
Inert ceramic balls are widely used in various industrial processes due to their excellent chemical stability, high mechanical strength, and thermal resistance. These small spherical ceramic pieces play a crucial role in many chemical and petrochemical applications, serving as catalyst supports, tower packing, and bed support media.
## Key Properties of Inert Ceramic Balls
The effectiveness of inert ceramic balls in industrial applications stems from their unique properties:
– High temperature resistance
– Excellent chemical inertness
– Superior mechanical strength
– Low water absorption
– Uniform size and shape
## Major Industrial Applications
### 1. Catalyst Support in Chemical Reactors
Inert ceramic balls are commonly used as catalyst supports in fixed-bed reactors. They provide a stable foundation for active catalysts while ensuring proper gas or liquid distribution throughout the reactor bed. Their inert nature prevents unwanted reactions with the process media.
### 2. Tower Packing in Distillation Columns
These ceramic balls serve as efficient packing materials in distillation and absorption towers. Their spherical shape promotes excellent fluid distribution and maximizes surface area for mass transfer between gas and liquid phases.
### 3. Bed Support in Filtration Systems
In filtration applications, inert ceramic balls create a stable support layer for filter media. They prevent the migration of finer filtration materials while allowing uniform flow distribution across the filter bed.
### 4. Heat Exchange Media
Due to their thermal stability, inert ceramic balls are used as heat exchange media in high-temperature processes. They facilitate efficient heat transfer while withstanding extreme thermal conditions.
## Advantages Over Alternative Materials
Compared to metal or plastic alternatives, inert ceramic balls offer several benefits:
– Longer service life in corrosive environments
– Better performance at elevated temperatures
– Higher resistance to mechanical wear
– Lower maintenance requirements
– More consistent performance over time
## Selection Considerations
Keyword: inert ceramic ball
When choosing inert ceramic balls for industrial applications, several factors should be considered:
– Process temperature range
– Chemical compatibility with process media
– Required mechanical strength
– Size and density specifications
– Pressure drop considerations
## Future Trends in Application
The use of inert ceramic balls continues to expand into new industrial sectors. Emerging applications include:
– Advanced renewable energy systems
– High-efficiency waste treatment processes
– Next-generation petrochemical refining
– Specialty chemical production
As industrial processes become more demanding, the role of inert ceramic balls as reliable, high-performance components will likely grow in importance across multiple industries.