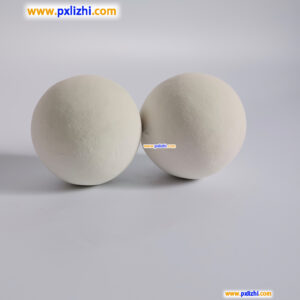
# Inert Ceramic Ball Applications in Industrial Processes
## Introduction to Inert Ceramic Balls
Inert ceramic balls are widely used in various industrial processes due to their excellent chemical stability, high mechanical strength, and thermal resistance. These small spherical ceramic materials play a crucial role in supporting catalysts, distributing gases and liquids, and protecting more expensive catalyst materials in reactors.
## Key Properties of Inert Ceramic Balls
The effectiveness of inert ceramic balls in industrial applications stems from their unique properties:
– High temperature resistance
– Chemical inertness
– Excellent mechanical strength
– Low water absorption
– Good thermal shock resistance
## Major Industrial Applications
Keyword: inert ceramic ball
### 1. Petrochemical Industry
In the petrochemical sector, inert ceramic balls serve as catalyst supports in reactors for processes such as:
– Catalytic reforming
– Hydrocracking
– Hydrodesulfurization
– Steam reforming
They help maintain proper gas distribution and prevent catalyst bed compaction.
### 2. Chemical Processing
Chemical plants utilize inert ceramic balls in:
– Fixed-bed reactors
– Distillation columns
– Absorption towers
– Scrubbers
Their chemical inertness makes them ideal for handling corrosive chemicals and high-temperature reactions.
### 3. Environmental Protection
In environmental applications, inert ceramic balls are used in:
– Flue gas treatment systems
– Wastewater treatment
– VOC (Volatile Organic Compounds) abatement
They provide support for catalysts that break down pollutants while withstanding harsh operating conditions.
### 4. Refining Processes
Oil refineries employ inert ceramic balls in:
– FCC (Fluid Catalytic Cracking) units
– Hydroprocessing units
– Sulfur recovery units
They help maintain proper flow distribution and protect downstream equipment from catalyst fines.
## Benefits of Using Inert Ceramic Balls
The advantages of incorporating inert ceramic balls in industrial processes include:
– Extended catalyst life by preventing mechanical degradation
– Improved process efficiency through better flow distribution
– Reduced pressure drop across reactors
– Protection of sensitive catalyst materials
– Lower maintenance costs due to their durability
## Selection Considerations
When choosing inert ceramic balls for industrial applications, consider these factors:
– Operating temperature range
– Chemical environment
– Required mechanical strength
– Size and shape specifications
– Thermal expansion characteristics
Proper selection ensures optimal performance and longevity in the intended application.
## Future Trends
The demand for inert ceramic balls continues to grow as industries seek more efficient and environmentally friendly processes. Advances in ceramic technology are leading to:
– Higher purity materials
– Improved thermal shock resistance
– Customized shapes for specific applications
– Enhanced mechanical properties
These developments will further expand the applications of inert ceramic balls in industrial processes.