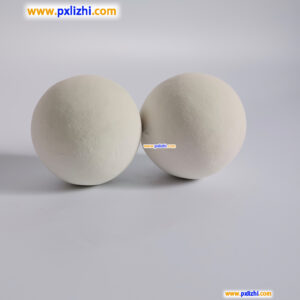
# Inert Ceramic Ball Applications in Industrial Processes
## Introduction to Inert Ceramic Balls
Inert ceramic balls are high-quality, chemically stable ceramic spheres that play a crucial role in various industrial processes. These small but mighty components are manufactured from high-purity materials like alumina, zirconia, or silica, offering exceptional resistance to thermal shock, chemical corrosion, and mechanical wear.
## Key Properties of Inert Ceramic Balls
The effectiveness of inert ceramic balls in industrial applications stems from their unique characteristics:
– High temperature resistance (up to 1800°C)
– Excellent chemical inertness
– Superior mechanical strength
– Low water absorption
– Uniform size distribution
– Exceptional thermal stability
## Major Industrial Applications
### 1. Petrochemical Industry
Inert ceramic balls serve as catalyst supports and bed separators in petroleum refining processes. They help distribute gases and liquids evenly while protecting more expensive catalysts from damage. Common applications include:
– Hydroprocessing units
– Catalytic reforming
– Fluid catalytic cracking
– Ethylene production
### 2. Chemical Processing
Chemical plants utilize inert ceramic balls in various reaction vessels and towers to:
– Improve gas/liquid distribution
– Prevent catalyst channeling
– Support catalyst beds
– Absorb thermal shocks in exothermic reactions
### 3. Environmental Protection
Inert ceramic balls contribute to cleaner industrial operations through:
– Waste gas treatment systems
– Desulfurization towers
– Denitrification processes
– VOC (volatile organic compounds) abatement
### 4. Steel and Metal Processing
The steel industry employs inert ceramic balls in:
– Blast furnace gas cleaning
– Coke oven gas purification
– Continuous casting processes
– Heat treatment furnace linings
## Benefits of Using Inert Ceramic Balls
The widespread adoption of inert ceramic balls across industries can be attributed to their numerous advantages:
– Extended equipment lifespan
– Improved process efficiency
– Reduced maintenance costs
– Enhanced product quality
– Lower energy consumption
– Increased safety in hazardous environments
## Selection Considerations
When choosing inert ceramic balls for specific applications, engineers should consider:
– Material composition (alumina content, purity levels)
– Size and shape specifications
– Bulk density requirements
– Crushing strength needs
– Thermal expansion characteristics
– Chemical compatibility with process media
## Future Trends
The inert ceramic ball market continues to evolve with:
– Development of nano-structured ceramic materials
– Improved manufacturing techniques for higher precision
– Custom formulations for specialized applications
– Integration with smart monitoring systems
Keyword: inert ceramic ball
As industrial processes become more demanding, inert ceramic balls will remain essential components for ensuring efficient, reliable, and sustainable operations across multiple sectors.