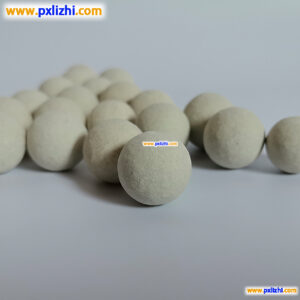
# Ceramic Ball Manufacturing Process and Applications
## Introduction to Ceramic Balls
Ceramic balls are precision-engineered spherical components made from various ceramic materials. These balls offer exceptional properties such as high hardness, wear resistance, chemical stability, and thermal insulation, making them valuable in numerous industrial applications.
## Manufacturing Process of Ceramic Balls
### 1. Raw Material Selection
The manufacturing process begins with selecting high-quality ceramic materials. Common materials include:
– Alumina (Al2O3)
– Zirconia (ZrO2)
– Silicon nitride (Si3N4)
– Silicon carbide (SiC)
### 2. Powder Preparation
The selected ceramic materials are ground into fine powders. The particle size distribution and purity of these powders significantly affect the final product quality.
### 3. Mixing and Binder Addition
The ceramic powder is mixed with organic binders and plasticizers to improve formability. This mixture is then homogenized to ensure uniform composition.
### 4. Forming Process
Several methods are used to form ceramic balls:
– Dry pressing
– Isostatic pressing
– Injection molding
– Extrusion
### 5. Green Machining
After forming, the “green” (unfired) ceramic balls undergo precision machining to achieve the desired spherical shape and dimensional accuracy.
### 6. Sintering
The formed balls are fired in high-temperature kilns (typically 1400-1800°C) to achieve full density and mechanical strength. This process causes significant shrinkage, which must be accounted for in the initial forming stage.
### 7. Precision Grinding and Lapping
After sintering, the balls undergo:
– Centerless grinding for size control
– Lapping for surface finish improvement
– Polishing for ultra-smooth surfaces
### 8. Quality Control
Each ceramic ball undergoes rigorous inspection for:
– Diameter tolerance
– Sphericity
– Surface roughness
– Mechanical properties
## Applications of Ceramic Balls
Keyword: ceramic ball
### 1. Bearings
Ceramic balls are widely used in high-performance bearings due to their:
– Low density (reducing centrifugal forces)
– High stiffness
– Corrosion resistance
– Ability to operate without lubrication
### 2. Valves and Pumps
In fluid handling systems, ceramic balls serve as:
– Check valve components
– Metering elements
– Pump bearings
### 3. Grinding Media
Ceramic grinding balls are used in:
– Ball mills
– Attrition mills
– Other size reduction equipment
### 4. Aerospace and Defense
Applications include:
– Gyroscopes
– Guidance systems
– High-temperature bearings
### 5. Medical Devices
Ceramic balls are used in:
– Orthopedic implants
– Dental applications
– Surgical instruments
## Advantages of Ceramic Balls
Property | Benefit
High hardness | Excellent wear resistance
Low density | Reduced centrifugal forces in rotating applications
Chemical inertness | Resistance to corrosion and chemical attack
High temperature stability | Performance in extreme environments
Electrical insulation | Useful in electronic applications
## Future Trends in Ceramic Ball Technology
The ceramic ball industry continues to evolve with:
– Development of new ceramic compositions
– Improved manufacturing techniques for higher precision
– Expansion into new application areas
– Integration with advanced materials in hybrid components
As technology advances, ceramic balls will likely find even broader applications across various industries, particularly where extreme conditions demand materials with exceptional performance characteristics.