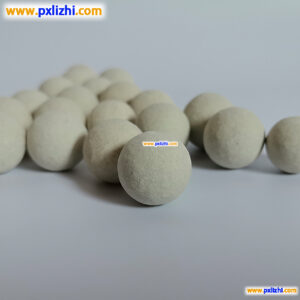
# Ceramic Ball Manufacturing Process
## Introduction to Ceramic Balls
Ceramic balls are precision-engineered spherical components used in various industrial applications, including bearings, valves, grinding media, and aerospace components. Their exceptional hardness, wear resistance, and thermal stability make them superior to traditional metal balls in many applications.
## Raw Material Selection
The manufacturing process begins with careful selection of raw materials:
– Alumina (Al2O3)
– Zirconia (ZrO2)
– Silicon nitride (Si3N4)
– Silicon carbide (SiC)
The choice of material depends on the intended application and required properties such as hardness, density, and chemical resistance.
## Powder Preparation
The ceramic powder undergoes several preparation steps:
1. Milling: Raw materials are ground to achieve uniform particle size
2. Mixing: Different powders are blended to achieve desired composition
3. Additives: Binders and lubricants are added to improve formability
## Forming Process
There are several methods to form ceramic balls:
### Dry Pressing
Powder is compressed in a die under high pressure to form green balls
### Isostatic Pressing
Powder is placed in a flexible mold and subjected to uniform pressure from all directions
### Injection Molding
Ceramic powder mixed with binder is injected into molds under high pressure
## Sintering
The formed green balls undergo sintering in high-temperature furnaces:
– Temperature ranges from 1400°C to 1800°C depending on material
– Process duration typically 2-10 hours
– Controlled atmosphere (air, vacuum, or special gas) prevents oxidation
## Finishing Processes
After sintering, ceramic balls undergo precision finishing:
### Grinding
Balls are ground to achieve precise spherical geometry and surface finish
### Lapping
Final surface finishing to achieve sub-micron level precision
### Polishing
Optional process for applications requiring ultra-smooth surfaces
## Quality Control
Each ceramic ball undergoes rigorous testing:
Keyword: ceramic ball
– Dimensional accuracy (sphericity, diameter)
– Surface finish measurement
– Hardness testing
– Density verification
– Visual inspection for defects
## Applications of Ceramic Balls
Finished ceramic balls find use in:
– High-performance bearings
– Check valves and flow control systems
– Grinding media for mills
– Aerospace components
– Medical implants and devices
## Advantages of Ceramic Balls
Compared to metal balls, ceramic balls offer:
– Higher hardness and wear resistance
– Lower density
– Better corrosion resistance
– Higher temperature stability
– Non-magnetic properties
– Electrical insulation
The ceramic ball manufacturing process combines advanced materials science with precision engineering to produce components that meet the demanding requirements of modern industries. Continuous improvements in manufacturing techniques are expanding the applications and performance capabilities of ceramic balls.