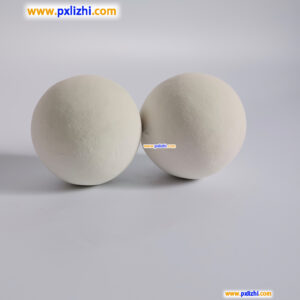
# Inert Ceramic Ball Applications in Industrial Processes
## Introduction to Inert Ceramic Balls
Inert ceramic balls are widely used in various industrial processes due to their excellent chemical stability, high mechanical strength, and thermal resistance. These spherical ceramic materials serve as inert support media in reactors, towers, and other process equipment, providing structural support while maintaining chemical neutrality.
## Key Properties of Inert Ceramic Balls
The effectiveness of inert ceramic balls in industrial applications stems from their unique combination of properties:
- High chemical inertness – resistant to acids, alkalis, and organic solvents
- Excellent thermal stability – can withstand temperatures up to 1600°C
- Superior mechanical strength – resistant to crushing and abrasion
- Low water absorption – maintains structural integrity in wet environments
- Uniform size distribution – ensures consistent performance
## Major Industrial Applications
1. Catalyst Support in Petrochemical Industry
Inert ceramic balls serve as essential support media for catalysts in fixed-bed reactors. They distribute gas or liquid flows evenly and protect catalyst particles from mechanical damage. Common applications include:
- Hydroprocessing units
- Reforming processes
- Isomerization reactors
2. Packing Material in Distillation Columns
These ceramic balls enhance mass transfer efficiency in distillation and absorption towers by:
- Creating uniform vapor-liquid contact
- Reducing pressure drop
- Preventing channeling effects
3. Thermal Insulation in High-Temperature Processes
The excellent thermal properties of inert ceramic balls make them ideal for:
- Furnace linings
- Kiln furniture
- Heat recovery systems
Keyword: inert ceramic ball
## Selection Considerations
When choosing inert ceramic balls for industrial applications, several factors should be considered:
Factor | Consideration |
---|---|
Size | Should match reactor/tower dimensions and process requirements |
Material Composition | Alumina content affects chemical resistance and strength |
Operating Temperature | Must withstand process temperature extremes |
Pressure Conditions | Crush strength should exceed operating pressures |
## Maintenance and Replacement
Proper maintenance of inert ceramic balls ensures long-term performance:
- Regular inspection for breakage or contamination
- Periodic cleaning to remove deposits
- Replacement when significant wear or damage occurs
- Proper loading techniques to prevent damage during installation
## Future Developments
The industrial applications of inert ceramic balls continue to expand with advancements in:
- Nanostructured ceramic materials
- Customized surface treatments
- Improved manufacturing processes
- Specialized formulations for extreme environments
As industrial processes become more demanding, inert ceramic balls will play an increasingly vital role in ensuring efficient and reliable operations across multiple sectors.