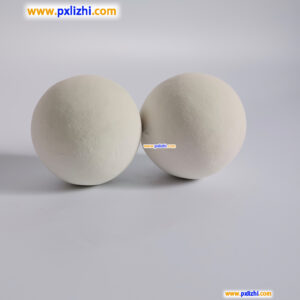
# Inert Ceramic Ball Applications in Industrial Processes
## Introduction to Inert Ceramic Balls
Inert ceramic balls are widely used in various industrial processes due to their excellent chemical stability, high mechanical strength, and thermal resistance. These small spherical ceramic pieces play a crucial role in supporting catalysts, distributing gases and liquids, and protecting catalyst beds in reactors.
## Key Properties of Inert Ceramic Balls
The effectiveness of inert ceramic balls in industrial applications stems from their unique properties:
- High temperature resistance (up to 1600°C)
- Excellent chemical inertness
- Superior mechanical strength
- Low water absorption
- Good thermal shock resistance
## Major Industrial Applications
1. Petrochemical Industry
Inert ceramic balls serve as catalyst supports in petroleum refining processes such as catalytic cracking, hydrotreating, and reforming. They help distribute reactants evenly across the catalyst bed while preventing catalyst particle movement.
Keyword: inert ceramic ball
2. Chemical Processing
Chemical plants utilize these ceramic balls in reactors for various synthesis processes. Their inert nature prevents unwanted reactions while providing structural support to the catalyst bed.
3. Environmental Protection
In air and water treatment systems, inert ceramic balls act as packing material in scrubbers and trickling filters, providing large surface areas for gas-liquid contact and pollutant removal.
4. Metallurgical Industry
High-temperature furnaces employ inert ceramic balls as heat storage media and for gas distribution in direct reduction iron processes.
## Advantages Over Alternative Materials
Compared to metal or plastic alternatives, inert ceramic balls offer:
- Better corrosion resistance
- Higher temperature tolerance
- Longer service life
- Lower maintenance requirements
- More consistent performance
## Selection Considerations
When choosing inert ceramic balls for industrial applications, consider:
- Operating temperature range
- Chemical environment
- Required mechanical strength
- Size and shape specifications
- Pressure drop requirements
## Future Developments
Research continues to improve inert ceramic ball technology, focusing on enhanced thermal conductivity, increased porosity for better gas distribution, and development of specialized formulations for extreme environments.