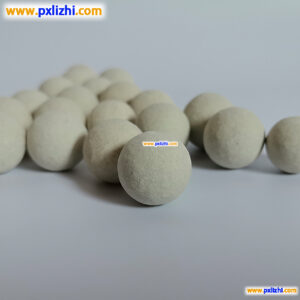
,文章要包含以下内容:1. Introduction to ceramic balls 2. Manufacturing process of ceramic balls 3. Applications of ceramic balls 4. Advantages of ceramic balls 5. Conclusion
html
Ceramic Ball Manufacturing Process and Applications
Introduction to Ceramic Balls
Ceramic balls are precision-engineered spherical components made from advanced ceramic materials such as alumina, zirconia, silicon nitride, or silicon carbide. These balls are known for their exceptional hardness, wear resistance, and thermal stability, making them ideal for demanding industrial applications. Ceramic balls are widely used in bearings, valves, grinding media, and other high-performance mechanical systems where durability and precision are critical.
Manufacturing Process of Ceramic Balls
The production of ceramic balls involves several meticulous steps to ensure high quality and consistency:
Keyword: ceramic ball
1. Raw Material Preparation
High-purity ceramic powders are selected and mixed with binders to form a homogeneous mixture. The choice of material depends on the intended application, with alumina and zirconia being the most common.
2. Forming
The mixed powder is shaped into spherical forms using methods like isostatic pressing, extrusion, or injection molding. This step ensures the initial spherical geometry of the balls.
3. Sintering
The formed balls are heated in a kiln at high temperatures (often exceeding 1500°C) to achieve densification and enhance mechanical properties. Sintering transforms the porous green bodies into solid, durable ceramic balls.
4. Grinding and Polishing
After sintering, the balls undergo precision grinding and polishing to achieve the desired surface finish and dimensional accuracy. This step is crucial for applications requiring tight tolerances, such as bearings.
5. Quality Control
Each ceramic ball is inspected for defects, dimensional accuracy, and surface quality. Advanced testing methods, including laser scanning and hardness testing, ensure compliance with industry standards.
Applications of Ceramic Balls
Ceramic balls are utilized in a wide range of industries due to their superior properties:
1. Bearings
Ceramic balls are commonly used in high-speed and high-temperature bearings for aerospace, automotive, and industrial machinery. Their low density reduces centrifugal forces, while their hardness extends bearing life.
2. Valves and Pumps
In corrosive or high-wear environments, ceramic balls serve as sealing or check valve components, offering resistance to chemical attack and abrasion.
3. Grinding Media
Ceramic balls are employed in ball mills for grinding and mixing materials in industries like mining, pharmaceuticals, and ceramics, where contamination-free processing is essential.
4. Medical Devices
Biocompatible ceramic balls, such as zirconia, are used in joint replacements and dental implants due to their wear resistance and compatibility with human tissue.
Advantages of Ceramic Balls
Ceramic balls offer several benefits over traditional metal balls:
- High Hardness: Resistant to wear and deformation, even under extreme loads.
- Corrosion Resistance: Impervious to rust and chemical degradation.
- Lightweight: Lower density reduces rotational inertia in high-speed applications.
- Thermal Stability: Maintains performance at elevated temperatures.
- Electrical Insulation