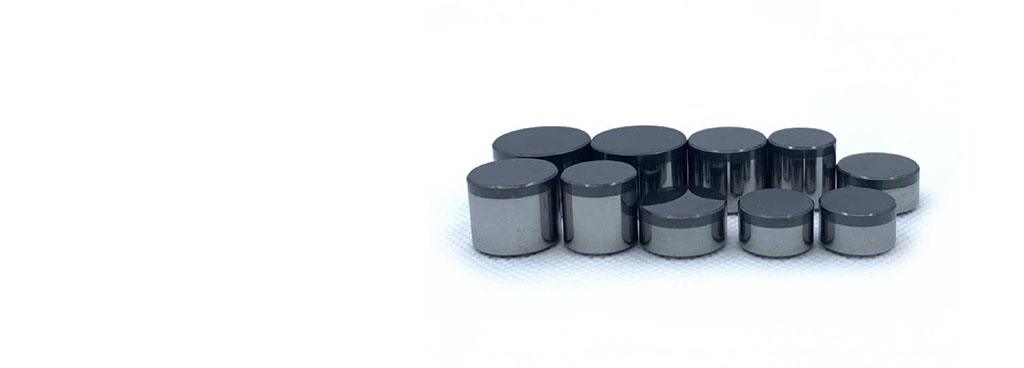
# PDC Bit Cutter Technology in Drilling Applications
## Introduction to PDC Bit Cutters
Polycrystalline Diamond Compact (PDC) bit cutters have revolutionized the drilling industry over the past few decades. These advanced cutting elements combine the hardness of diamond with the toughness of tungsten carbide, creating a superior cutting solution for various drilling applications.
The Science Behind PDC Cutters
PDC cutters consist of a layer of synthetic diamond particles bonded to a tungsten carbide substrate under high pressure and temperature. This manufacturing process creates a cutting element that offers exceptional wear resistance and thermal stability, making it ideal for demanding drilling operations.
## Advantages of PDC Bit Technology
The implementation of PDC cutter technology in drilling bits provides numerous benefits:
- Superior wear resistance compared to traditional roller cone bits
- Increased rate of penetration (ROP) in most formations
- Longer bit life, reducing the need for frequent bit changes
- More consistent performance throughout the bit’s lifespan
- Reduced vibration and improved borehole quality
Applications in Various Drilling Environments
Oil and Gas Drilling
PDC bits have become the preferred choice for many oil and gas drilling operations, particularly in softer to medium-hard formations. Their ability to maintain sharp cutting edges throughout extended drilling intervals significantly improves operational efficiency.
Geothermal Drilling
The thermal stability of PDC cutters makes them particularly suitable for geothermal applications where high temperatures are encountered. Their wear resistance also proves valuable in abrasive formations common in geothermal wells.
Mining and Construction
Beyond traditional oilfield applications, PDC cutter technology has found success in mining and construction drilling. The bits’ durability and cutting efficiency translate to cost savings in these industries as well.
Keyword: pdc bit cutter
Recent Technological Advancements
Recent developments in PDC cutter technology include:
- Improved diamond table designs for enhanced impact resistance
- Advanced thermal management systems to prevent heat damage
- Customized cutter geometries for specific formation types
- Hybrid bit designs combining PDC and roller cone elements
Future Outlook for PDC Technology
As drilling operations continue to push into more challenging environments, PDC cutter technology is expected to evolve further. Research focuses on developing even more durable cutters capable of handling ultra-hard formations while maintaining cost-effectiveness. The integration of smart technologies with PDC bits may also provide real-time performance monitoring in future drilling operations.
The ongoing refinement of PDC bit cutter technology ensures its position as a cornerstone of modern drilling practices across multiple industries.