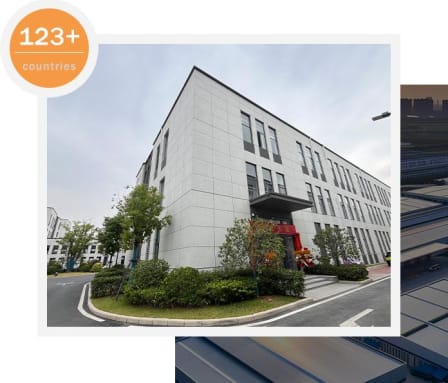
html
PDC Cutter Performance Optimization in Drilling Operations
Polycrystalline Diamond Compact (PDC) cutters have revolutionized the drilling industry with their superior wear resistance and cutting efficiency. However, maximizing their performance requires careful optimization of several key factors.
Understanding PDC Cutter Fundamentals
PDC cutters consist of a synthetic diamond layer bonded to a tungsten carbide substrate. The diamond layer provides exceptional hardness while the carbide substrate offers structural support. This combination makes PDC cutters ideal for challenging drilling environments.
Key Factors Affecting PDC Cutter Performance
1. Cutter Geometry
The shape and size of PDC cutters significantly impact drilling efficiency. Common geometries include:
- Conical cutters for hard formations
- Chisel-shaped cutters for directional drilling
- Round cutters for general applications
2. Diamond Layer Quality
The diamond layer’s thickness, grain size, and bonding quality determine cutter durability. High-quality diamond layers with uniform grain structure provide better thermal stability and wear resistance.
3. Back Rake Angle
The angle between the cutter face and the formation affects cutting efficiency. Optimal back rake angles typically range between 10-20 degrees, depending on formation hardness.
Optimization Strategies
Keyword: cutter pdc
Formation-Specific Cutter Selection
Matching cutter characteristics to formation properties is crucial. Soft formations benefit from sharper cutters with higher back rake angles, while hard formations require more durable cutters with lower back rake angles.
Thermal Management
Excessive heat is a primary cause of PDC cutter failure. Implementing proper cooling systems and optimizing drilling parameters can significantly extend cutter life.
Hydraulic Optimization
Effective fluid circulation removes cuttings and cools the bit. Proper nozzle placement and flow rates ensure efficient cutter cleaning and cooling.
Emerging Technologies
Recent advancements in PDC cutter technology include:
- Novel diamond synthesis techniques for improved thermal stability
- Advanced cutter coatings for reduced friction
- Hybrid cutter designs combining PDC and other materials
Conclusion
Optimizing PDC cutter performance requires a comprehensive approach considering cutter design, formation characteristics, and operational parameters. By implementing these optimization strategies, drilling operations can achieve significant improvements in rate of penetration, bit life, and overall drilling efficiency.